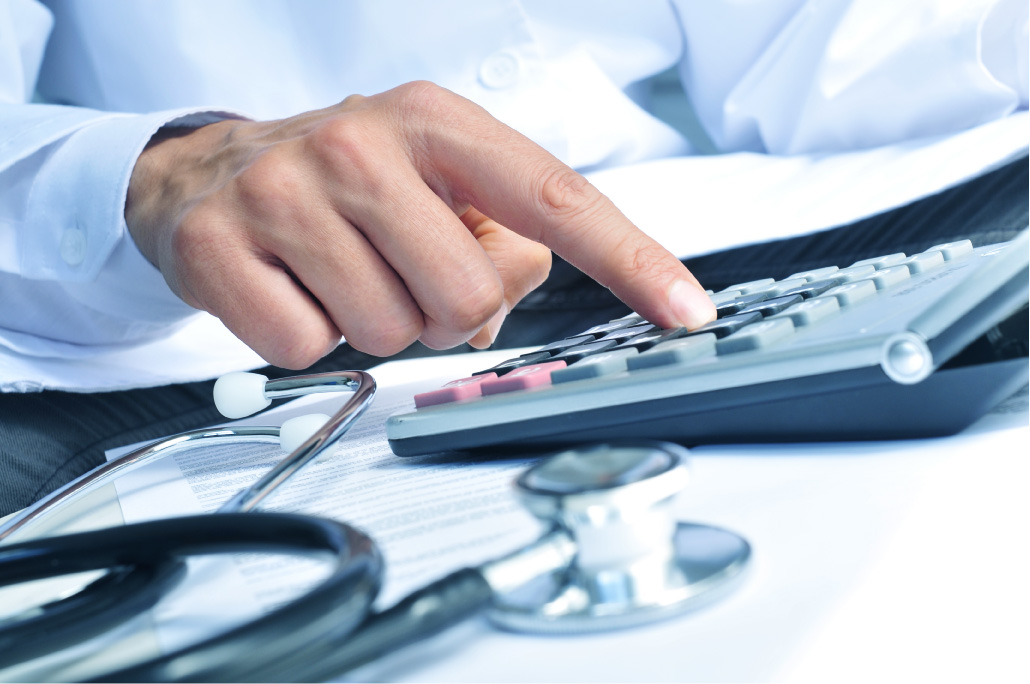
For an ASC leader, understanding the financial impact of each surgery performed in an ASC is critical to the facility’s success. To achieve this, you must have detailed, accurate data on surgical costs and reimbursements.
Most facilities have software that produces reports which assist with gathering and modeling data. Depending on the resources available at your facility, the difficulty in gathering and using case-costing data will vary.
Avoiding ‘bad’ data
Some management companies, like Pinnacle III, employ a data analyst to provide tools to analyze the cost and reimbursement of cases. However, even with the help of a data analyst, the analysis will only be helpful if the data collection process is accurate and thorough. A common saying among data scientists is, “Garbage in equals garbage out.” For ASCs, if the person pulling the data does not have accurate data to work with, case-costing will be inaccurate.
Here are a few ways to avoid producing bad data.
- Ensure staff are entering valid data into your software and paying attention to details. Educating staff about the impact of their role in this process is key. Staff mistakes, such as entering equipment cost as supply, can falsely inflate the cost of the case in your analysis. These mistakes are easily avoided by focused staff members who have received adequate training on their function and impact.
- Update staff compensation. If pay rates aren’t current in your software, the labor costs associated with a case will be incorrect.
- Engage your materials personnel. The material personnel are vital to keeping information current and accurate. Supply pricing changes must be up-to-date in your software.
- Keep preference cards current. Make sure hold items are not listed as open. Ensure standard items used on every surgery are correct. This will avoid waste and reduce errors when accounting for what was used during each surgery.
- Don’t forget supplies used outside of the OR. The supplies used in pre-op and PACU for a patient can seem insignificant. However, accounting for them with the surgery ensures general supply expenses spread among all cases is reduced. Create a pre/post bundle price for each type of surgery that gets added to the supply used. And don’t forget to include anesthesia supplies and drugs, which are often overlooked.
- Include everything with a fee. Often there will be a charge for something, such as rental for a laser or a tray drop-off, that can be easily left out. If certain items are always used and the fee is known, add them to the preference card and include the fee in your software. Educate staff to facilitate understanding about which items carry a fee to ensure those costs are added to the case.
- Accurately capture implants and instrumentation. Avoid including reprocessed items as an expense. Ensure fees are not attached to reprocessed instruments or they could be charged to the case as a supply used. Ensure implants used are reflected in your software with the appropriate price.
Final tips for case-costing analysis
There are obvious costs to capture, however, some items may be overlooked, particularly if you are not utilizing a data analyst. Some things to remember when gathering case-costing data are:
- Include total visit time as well as OR time. The length of time the patient spends in the facility from admission to discharge is an important factor in the overall cost of a case.
- Use your P&L to tie-in general expenses to be allocated among all cases as an indirect expense.
- Include the payor mix. This is very important as the payor mix can be a contributing factor to variances among surgeons.
- There is never too much detail. The process is tedious, but the result will benefit the ASC in many ways. The more ways the data can be sorted, the easier it will be to identify inefficiencies, waste, spending variances, long recoveries, and a variety of trends.
- Separate supplies and implants. This will allow you to compare surgeons by case and identify opportunities for savings and standardization.
Once the data is gathered, configure it in a way that will allow you to study it from multiple angles (e.g., via a spreadsheet program). Begin with a broad view – by specialty, physician, CPT, or payor, for example. Then examine the subsets – perhaps by specialty/by physician or by physician/by CPT. If you notice significant variances, dig deeper to determine the cause. As you study the data you may find errors. Rather than being frustrated by inaccuracies, use errors as an opportunity to refine your processes and/or systems. Avoid sharing data with your surgeons until you are confident it is accurate. Seek their insights when sharing the information; they may be able to point to additional areas to investigate prior to making operational decisions based on the data.
As you refine your processes and systems, keep your staff and surgeons in the feedback loop. Addressing errors as they arise will create a more seamless process that allows you to focus on other improvement opportunities.
Stay tuned for the second-part of my case-costing blog series. In my follow-up blog, I will further discuss best-practices for analyzing case-costing data. I will also delve into ways to utilize case-costing data, and the benefit of engaging surgeons in the process.
Lori Tamburo, Director of Operations